Download this handy 1-page information sheet!
MANAGING ANISOTROPY IN
ARCHITECTURAL GLASS
NEED TO TAKE THIS PAGE WITH YOU?
What is Anisotropy in Architectural Glass?
Anisotropy can go by many names: leopard spots, iridescence, birefringence; but whatever you choose to call it, the results are the same. Anisotropy is a visible shadow like pattern that is visible in polarized lighting conditions and most often in reflection, meaning it will typically only be visible on the exterior lites of a building.
Visible anisotropy on exterior glass
In its native condition, light shoots off in all directions, but polarized light waves are essentially “clean light” or light that is filtered to allow rays to oscillate along a single plane.
The effect of a polarized medium
There are certain conditions that cause polarization of light such as shiny surface reflections, blue sky, water reflections, or even on wide viewing angles to reflected surfaces. Of course, the sure-fire way to polarized light is through polarized sunglasses.
Page Menu
UNDERSTANDING
FINAL THOUGHTS
Why does anisotropy occur in architectural glass?
Differences in area stresses create regions with slightly different refraction indexes. Those changes in the speed of light produce optical patterns called anisotropy. A practical example: Have you seen the spots all over your car’s windows? That is anisotropy, and you can see the areas of high and low stress caused by the quenching air jets compressing the material to a different stress.
These inhomogeneities split a single polarized light ray into two perpendicular rays that are slighting out of phase, and without getting into the science of waveforms, the out of phase light will produce the visual disparity we call anisotropy.
There are no two ways around it. You WILL have anisotropy in heat-treated glass, but the amount is largely based on two variables:
- The oven and quench configurations of the oven
- The tempering operator’s skill in heating and cooling glass uniformly.
More simply, the amount of anisotropy you receive figures purely on the quality of your fabrication partner. Until recently, both the glass fabricator and project stakeholders just had trust they were producing and receiving the least anisotropy. We will explore how new standards are improving the outcomes for all parties.
WHAT YOU NEED TO KNOW
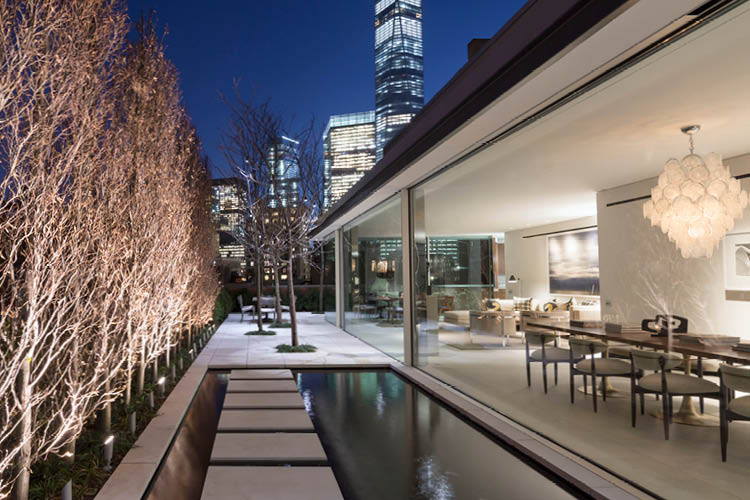
Bigger glass = thicker glass and heat-treatment. Anisotropy in high-end residential, retail, or commercial spaces is unwanted.
Why you should care about anisotropy
As architects and designer demand larger architectural glass to fit with design trends, the thickness of glass must increase, and heat-treatment becomes necessary to maintain strength, safety, and durability of the lite.
In tandem, architects are becoming acutely aware and sensitive to anisotropy, now including references to the phenomenon in project specifications.
However, the specification and measurement of anisotropy is often misunderstood. For example, at AGNORA we have seen requests for zero anisotropy in heat-treated glass. This wide variation in the understanding of anisotropy can lead to undeliverable specification, a protraction in quality, and even costly legal disputes surrounding the final output of the glass vs the perceived expectation of the architect or other project stakeholders.
There is a way to curb misinformation while managing and agreeing on a single expectation. The way is an objective single measurement of anisotropy.
Standardization is the answer - ASTM C1901 Standard
The affordability, usability and ubiquity of high-performance scanning equipment has exploded over the last several years, allowing fabricators the opportunity to scan and perfect glass recipes to best limit anisotropy.
However, measurement is not enough. Education of all stakeholders is crucial in understanding anisotropy so that it may be properly specified and managed. Fabricators must also use a repeatable, globally recognized test method to ensure industry wide consistency.
ASTM C1901-21 is a new standard that provides fabricators a systemized measurement method that is repeatable, traceable, and global in nature. The final output is described in a fundamental physical unit, the nanometre (nm), that can be agreed upon and utilized by architects and designer in their final specification.
Simply, with C1901-21 it is possible to objectively improve the heat-treating process and agree on a quantifiable anisotropy value between project parties.
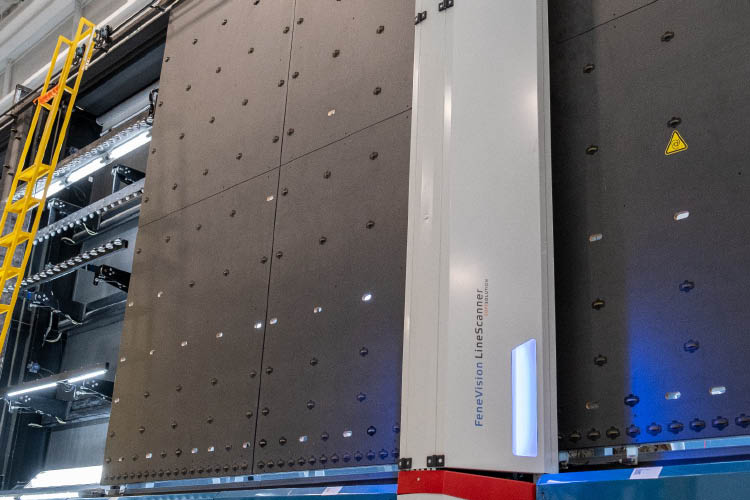
High-quality scanners are becoming more widely used by fabrictors; useful when combined with the ASTM C1901 standard.
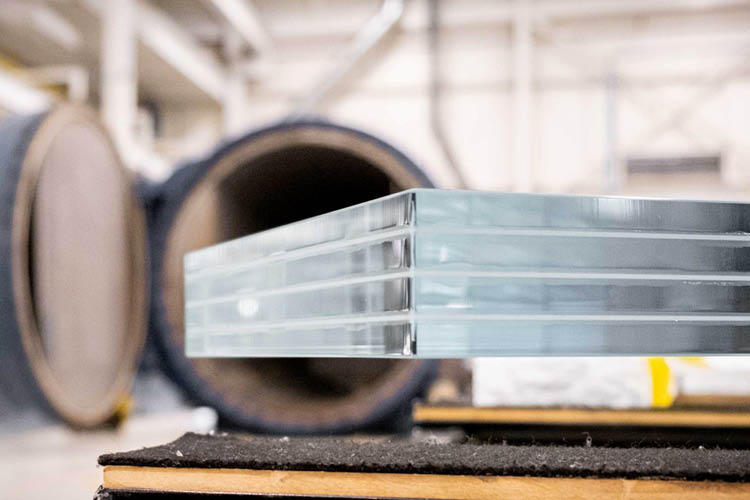
Lamination is a fantastic option for economically increasing the thickness of glass.
The Other Answer - Annealed Glass
We established that as glass become bigger, so to does their thickness to encourage strength and reduce deflection. The answer is typically heat-treated glass, but small glass can be made thicker through lamination.
One can avoid anisotropy and visual distortion from the tempering oven (i.e. roller wave) all together by using annealed glass, and laminating it to a desired thickness. This process is an often more economical form of acquiring BIG architectural glass.
Combined with modern day interlayers such as Kurarays SentryGlas (up to 4x stiffer than conventional PVB). One can achieve almost equal strength to that of thick, heat-treated glass while eliminating all visual anomalies found in the heat-treating process. Further, laminated annealed glass maintains its structure in the event of a breakage, and is not prone to NiS spontaneous breakage, two additional safety and monetary benefits.
FINAL THOUGHTS
Changing the industry approach to heat-treating glass
If you’re specifying heat-treated glass, you WILL HAVE anisotropy, but as of 2021, there are not only the tools, but a standard in place to produce an agreeable outcome for each party.
Modern day interlayers provide a robust, clear, strong, and safe solution to thicken glass lites and is worth considering.
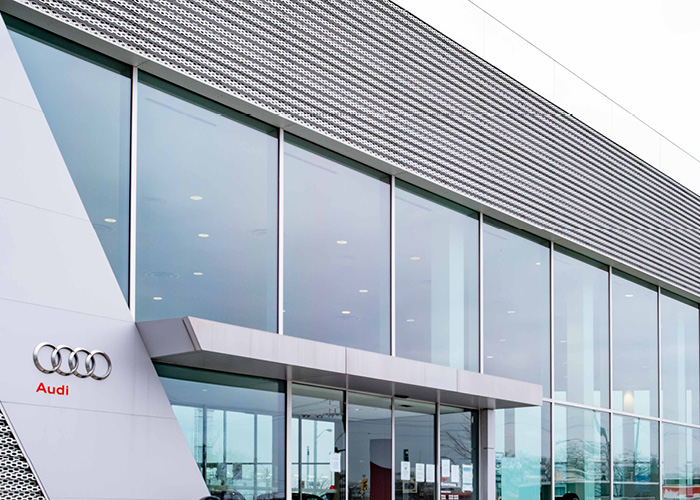
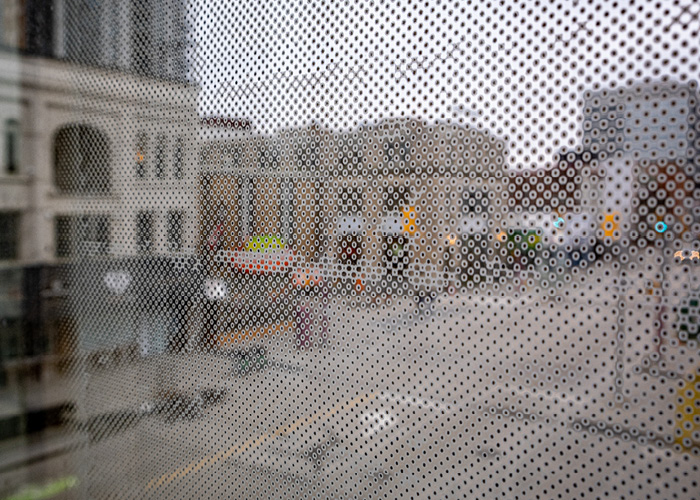
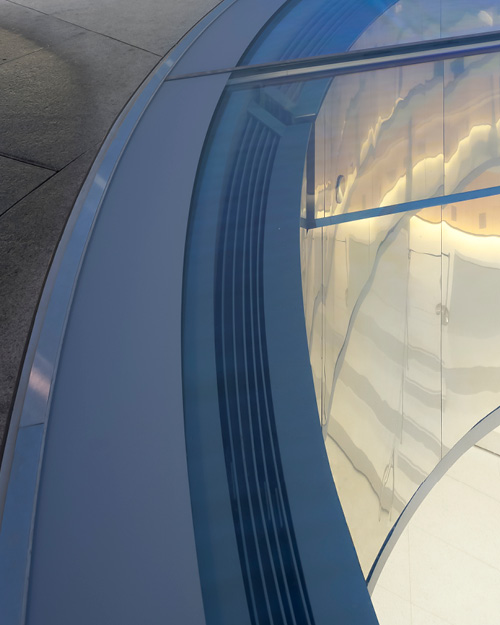
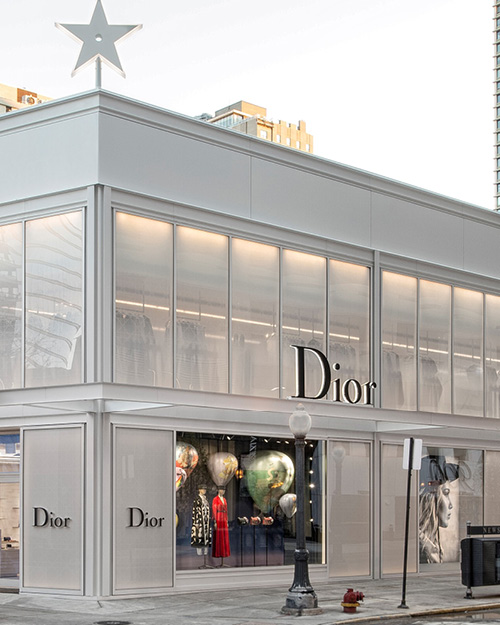
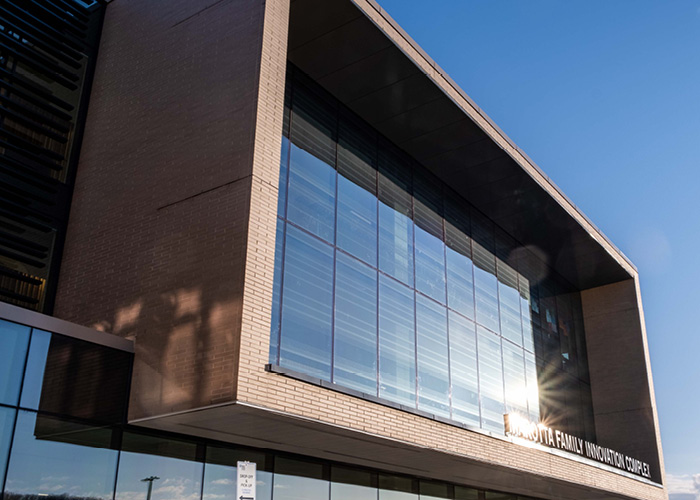