Precision Lamination
The lamination process is one of the most comprehensive procedures in a fabricator’s facility. The process of lamination requires patience, precision, and highly skilled operators to care and assemble massive lites of glass to incredible tolerances. Learn the reasons why lamination can save money and improve the overall performance of architectural glass.
Laminated glass is not new, it was invented in 1903 by the French chemist Édouard Bénédictus (1878–1930). Édouard started the Société du Verre Triplex making laminated windshields in 1911! Unfortunately, the bonding agent turned yellow and was too stiff. It took a few years for Monsanto to industrialize polyvinyl butyral (PVB) invented by Canadian chemists Howard Matheson and Frederick Skirrow in 1937. Laminated car windshields became mainstream after the second war.
The Importance of Lamination
There are many profound reasons why lamination is required. Lamination provides an effective solution for the following factors:
Safety
Obviously, safety is the first objective: protect occupants of flying debris by keeping broken fragments together. Following an automotive lead, it took 25 years for the architectural world to start using PVB laminated safety glass in buildings.
In North America, ANSI Z97.1 is the standard describing the safety of laminates. As a rule of thumb, it takes at least 0.030” (0.76) mm of PVB to meet the Z97.1 standard.
Security
By combining layers of glass and interlayers, different levels of security can be achieved. Starting with resistance to a baseball bat hit to stopping Kalashnikov bullets. See our past article on storefront security.
A substitute for thick, expensive monolithic glass
As glass increases in size, so does its thickness requirement to meet wind load condition. Thick float glass (>1/2”-12 mm) costs more than its laminated equivalent. For example, a 3/4” – 19 mm Fully Tempered (FT) lite will cost 55 % more than its annealed laminated cousin (3/8” / 0.030”/ PVB 3/8”– 1010.2). Using lamination and annealed glass to create thickness is clearly a desirable solution as it also eliminates spontaneous breakage risks, the need to Heat Soak Test (HST), optical distortions and anisotropy.
UV protection
A benefit of lamination is its ability to filter out harmful UV that can impact and fade surrounding furniture and objects. In fact, PVB or SentryGlas interlayers can reduce more than 98% of UV rays.
Solar protection
By embedding a solar control high performance coating, you can obtain an excellent SHGC. For example, a 3/8” / 0.030”/ PVB 3/8”– 1010.2 laminate can offer a VLt of 67% and a SHGC of 0.36.
Structural application
The advent of stiff interlayers like SentryGlas and DG-41 provides structural support for use in stairways, bridges, railings, and fins among other custom requirements. With a shear modulus that can be two orders of magnitude (100x) stiffer than traditional PVB, SentryGlas is an effective structural component.
Decorative application
AGNORA stocks a host of interlayers as we are required to be nimble, often creating custom or oversized solutions. AGNORA can also laminate fabrics or metal meshes for very special effects.
Do you need colour or whites in your glass? AGNORA carries a broad range of Vanceva colour interlayers that can be mixed and matched to create striking, permanent visuals.
Biggest On This Side Of The Pond
AGNORA is known for a lot of things such as custom, high-quality glass, and precision workmanship. We’re also known for BIG glass, and as such our lamination line is the largest in North America capable of handling glass 300” L x 130” W and thicknesses from ¼” to 4” (max weight per piece: 5500 Lb – 2500 kg).
The fully automated line cleans and preps each glass lite within a temperature-controlled clean room. Operators are responsible for the final alignment and application of interlayers. From there, the freshly laminate glass “sandwich” is sent through an advanced nip process which essentially heats and squeezes the laminate to expel air.
Finally, AGNORA’s massive autoclave is used to fully heat and pressurize the glass in order to alleviate any air, and firmly cement the interlayer to the glass substrate through 190 PSI – 13 bar of pressure and 275 °F – 135 °C.

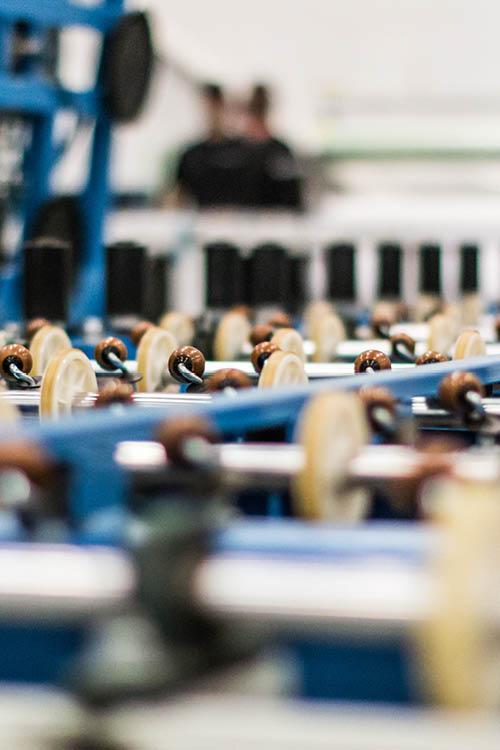
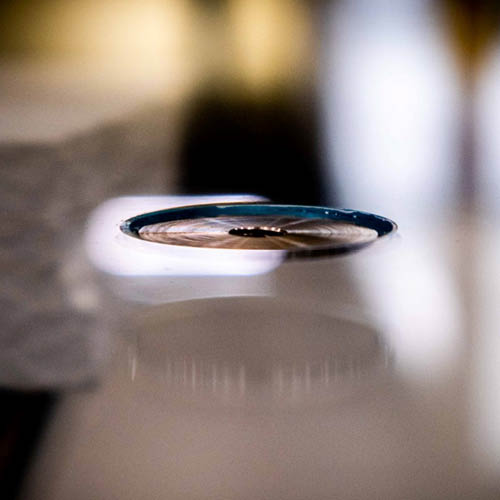
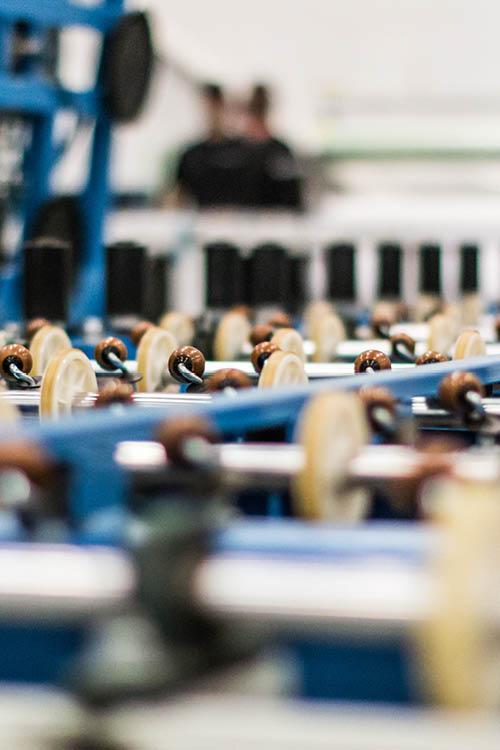

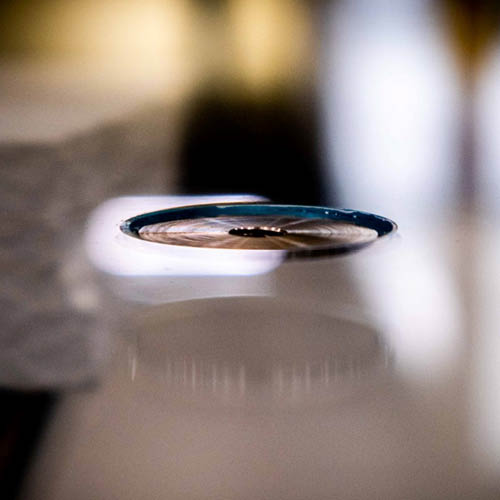
Big On This Side Of The Pond
AGNORA is known for a lot of things such as custom, high-quality glass, and precision workmanship. We’re also known for BIG glass, and as such our lamination line is the largest in North America capable of handling glass 300” L x 130” W and thicknesses from ¼” to 4” (max weight per piece: 5500 Lb – 2500 kg).
The fully automated line cleans and preps each glass lite within a temperature-controlled clean room. Operators are responsible for the final alignment and application of interlayers. From there, the freshly laminate glass “sandwich” is sent through an advanced nip process which essentially heats and squeezes the laminate to expel air.
Finally, AGNORA’s massive autoclave is used to fully heat and pressurize the glass in order to alleviate any air, and firmly cement the interlayer to the glass substrate through 190 PSI – 13 bar of pressure and 275 °F – 135 °C.
AGNORA is your partner for all things oversized, custom and technical.
All of the current technology used by AGNORA adds up to these key benefits for our customers:
- The only glass fabrication line to laminate 299” x 130” x 4”
- A highly diversified lineup of laminates that work for every application
- A very high level of final precision: +- 0.5mm.
Our ability to output highly complex shapes and structures, with a high-level of precision, and the ability to produce jumbo laminates make AGNORA an idea choice for:
- Oversized, high-quality glass laminates
- Custom, structural glass laminates used for exhibits, artwork, stairways, bridges, and railings
Our selection of laminate and commitment the most current technology and innovation ensures years of trouble free, highly durable architectural lites.