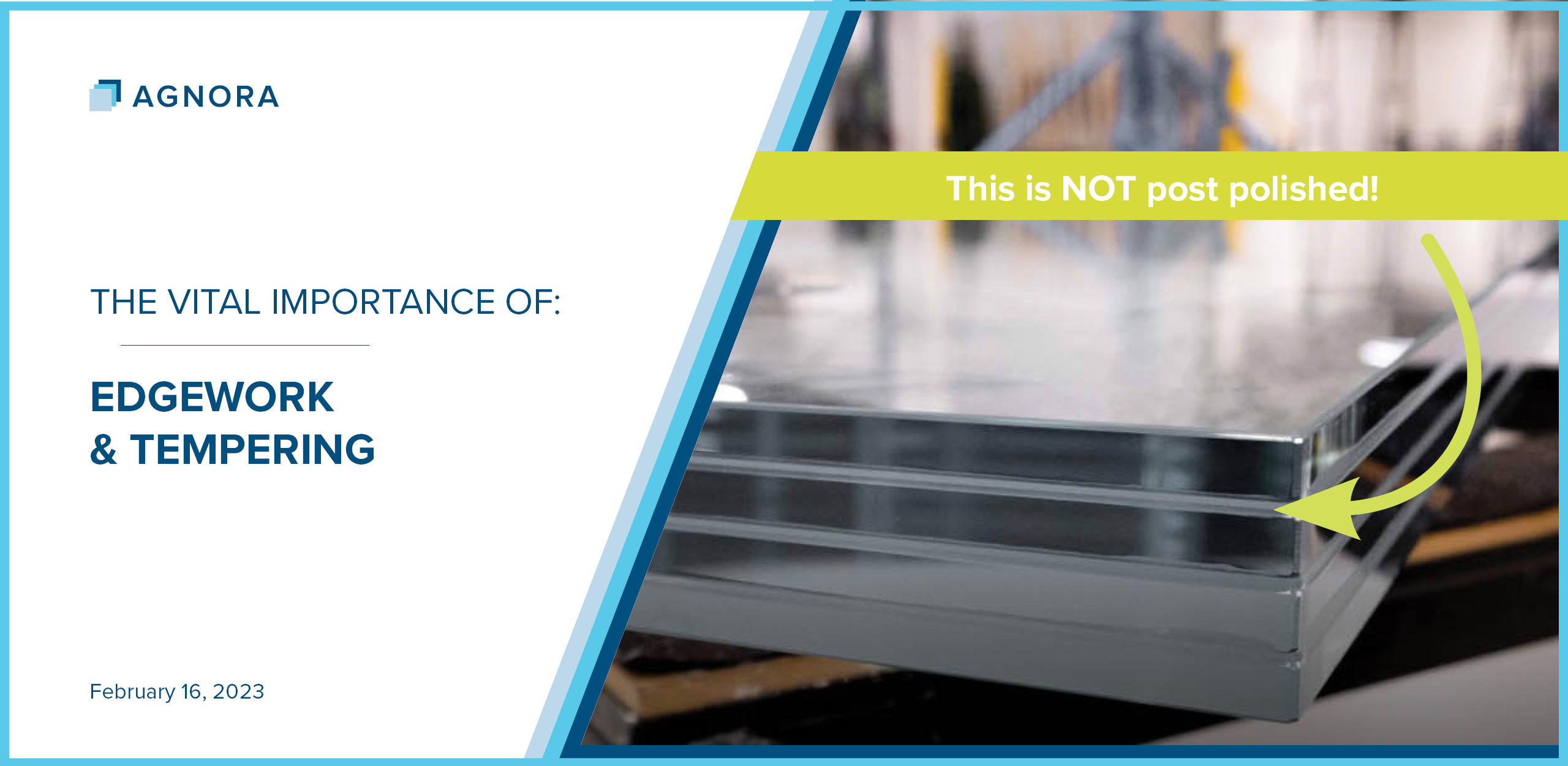
Thursday February 16, 2023
The Relationship Between Glass Edgework & Tempering
The interplay between edgework quality and tempering consistency is key to perceptively distortion-free glass that maintains a high degree of bending strength and overall stability. This article explores the effectiveness of these concepts and will allow you (the glazier, architect, owner, or specifier) to make more informed decisions about fabrication partners, and at minimum, be able to ask informed questions of your current processor.
Often when working with architects, or delivering an educational session we get asked, “How do you make glass that large, that flat?” It is usually an involved response, and is thus, the basis of this article to help illustrate empirically, how this level of precision is reached.
Supporting Videos
Why and how glass is tempered?
The strength of a material is the value of the stress at which it will deform permanently. Glass naturally is quite brittle, and brittle materials fracture rather than deform.
We must clarify a few terms to move forward:
1) Tensile stress: Is the pulling force applied to an object causing elongation.
2) (Ultimate) Tensile strength: Is the maximum tensile stress that the object can withstand before finally breaking.
3) Compressive stress: Is the pushing force applied to an object causing compaction.
4) (Ultimate) Compressive strength: Is the maximum compressive stress that the object can withstand before permanently deforming and/or permanently reducing volume.
Interestingly glass has a tremendous compressive strength to that of other structural components, in the order of 1000 MPa (10 tonnes required to deform/shatter a 1cm cube).
Thus, tensile stress is actually the characteristic that determines how “strong” glass is. This is why annealed glass is easy to break. The mechanics behind glass breakage are interesting. When a load is placed on a glass panel, and deflection occurs, one face will be under compression (good!) and the other will be under tension (bad!). Resistance to breakage on the compression side will be high, but since glass’ tensile strength is exceeding low, the glass will shatter due to the tensile stress exceeding the glass’ tensile strength, on one side (the outside of the bend).
We can solve this by…adding some compression! I.e., Tempered Glass!
Tempered glass exists in a state of both compression and tension. Glass is heated to an almost plastic state and rapidly cooled by compressed air in a quench, causing a compression layer or “toughened skin” to form, while the “core” or the glass draws (is sucked) outward into tension. When the glass exits the furnace, these two forces are in equilibrium.
{pic} One can think of the compression (pushing/compacted) layer surrounding the outside of the glass as a hard “skin” that increases the glass’ strength overall by not letting a deflected surface go into tension and exceed its tensile strength (it will eventually if you bend it too much).
We can start to see the value in tempering: Adding compressive strength to the glass will allow for much greater deflection before failure. In fact, annealed glass fails under loads roughly 20-40 MPa depending on how close the edge you measure. Heat treating, and adding compressive strength increases resistance to breakage between 120 to 200 Mpa, a 3x to 5x increase.
Because the compression layer is effectively higher density due to compaction, a balanced compression zone will only be 21.1% of the total thickness of glass. The percentage swings lower with thick material and slightly higher on thinner substrates such as 4mm. Refer to figure 1. for a depiction of glass thickness vs. compression zone area.
Tempering and the outdoors – Reduce the risk of thermal fracture
Thermal fractures occur at the edge of the glass when the stress that is generated in the main body of glass is greater than the edge strength. For every one-degree difference in temperature between the edge and main body of the glass, a stress of approximately 0.62 MPa is generated. Therefore, where temperature differences of 20 to 30°C exist from one part of a panel to another, stress levels of 12 to 19 MPa can easily form. In annealed glass, introducing levels of stress over these magnitudes will likely cause breakage.
Finally the edgework! Why does edgework influence tempered glass?
FINALLY, the edgework! Why does edgework influence tempered glass?
We have effectively strengthened glass by adding a layer of compression. So long as the tensile force does not exceed the added compressive strength (>120-200 MPa) the glass will not break.
But will it?
Now we must factor in cracks. More specifically microcracks.
Surprisingly, heat treated glass will be strongest along the edges. But if cracks exist, they can and will propagate and widen, eventually causing too much stress and failure. Therefore you may see glass (that is not broken by impact (i.e., tensile stress that is too high or Nickle Sulfide) breakage originating from the edge. For the best durability of all glass components, great care should be taken in edgework to eliminate all microfractures and the risk of failure in the field.
The below image illustrates the surfaces resulting from several types of finishing. Note the manually arrised edge versus machine polished. The ability for cracks to form under the manual conditions are much higher.
Why post temper polish is not a good idea!
As we’ve established, tempered glass combined with smooth surfaces are the “industry best” choice, but what about creating a mirror-finished edge and chamfer AFTER tempering rather than BEFORE? This area is still a grey zone for fabricators, but more attention is being applied to this subject to help ensure consistent material strength and safety. All that we have learned will now be distilled to three reasons why not to post-temper polish:
- 1. Not only are you removing compressive strength, but as mentioned, the type of finish will play an additional role in post-tempered glass longevity as microcracks may be introduced from manual arising or machine grinding. Normally, the act of tempering softens and helps to close cracks on the glass surface, thus reintroducing them is suboptimal.
2. Strange things happen near the edge of tempered glass. The tension component of the glass“squishes” out toward the edge like a PB&J sandwich being held too tight. The 21.1% of compression layer thickness does not hold true for the edge. In reality, there is much less compression layer to work with, and removing even a little compression layer can greatly reduce overall strength in a non-linear way compounding the overall strength loss.
- 3. In 2016, the ASTM E1300 standard was modified to determine load resistance of glass when both its thickness and residual compressive surface stress (RCSS) are known. This allows for an estimate of the reduced strength of the lite, dependent on the amount of compression zone removed. Though the measurement is for the surface of the glass, it remains a cautionary tale of strength reduction from any post-temper polish treatment. In fact, measured strength reduction was above even conservative estimates values of 25% (for 4% | 9/1000” | .22mm removal).
- 4. BONUS – Even ASTM C1048, the standard which everyone defaults to says: 7.7.1 Fabrication Guidelines— Heat-strengthened and fully tempered flat glass cannot be cut after the heat-treating process. Fabrication altering the glass surface, thickness, or edges shall be performed before heat-treating to avoid a reduction of glass strength
The Good News: You can get perfect-polish exposed edge.
By now, you may be thinking there is no way to get high-quality, high-strength, exposed edge with high-polish. Heaven forbid laminated glass!
How do you manage laminated, perfect-polish, exposed edgework?
Most high-quality fabricators will be able to produce a perfect polish, laminated edge for their customers without resorting to post-temper edgework. It can be done; However, it takes great care, patience, and experienced experts to do it. The best thing you can do is talk to your fabricator. Ask what they do and how they finish exposed edges.
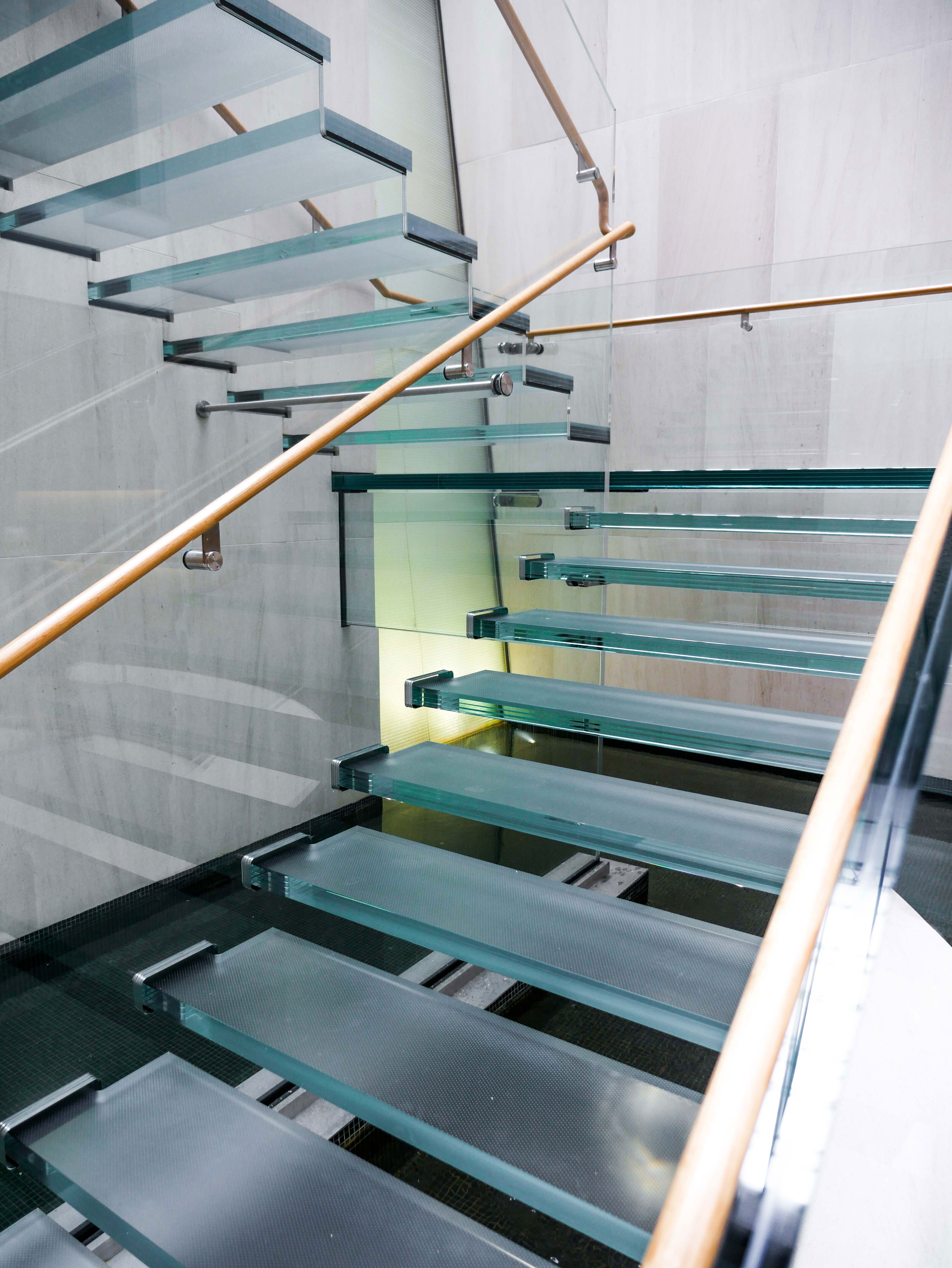
How can you make near “distortionless” tempered glass?
Distortion that occurs in glass comes in three varieties:
– Overall Bow
– Edge Curl
– Roller Wave
To effectively reduce the amount of physical distortion that occurs to the glass lite, the tempering operator may choose to heat the glass more slowly and with less heat to minimize the glass’ “plasticity” and ability to deform over the rollers.
However, tempering “on the line” comes with considerable breakage risk, as the quench may not be able to compress the material enough causing the tension zone to outpace and break the lite in the quench (remember the compression and tension forces must be in equilibrium).
On-line scanning technology and years upon years of data surrounding time of year, atmospheric pressure, material type and material thickness, allow experienced operators to optimize tempering recipes to create the level of clarity you would expect from a premiere glass fabrication partner.
Tying it all together! The Conclusion!
To receive high-quality, low-distortion glass that carries the original level of tempered strength, fabricators that fully grasp and understand the importance of precision finished surfaces and impeccably developed tempering recipes. This means that fabricators who:
- Finishes the glass to a machine ground or machine polished edge before the tempering process
- Polishes blemishes or inconsistencies from the glass before tempering
- Does not post-temper polish glass edges that are laminated or part of an assembly
- Temper “on-the-line” to limit plasticity and thus low resulting roller wave and anisotropy values
It may sound simple – just ensure that the fabricator is following the correct order of processes. However, that’s not always the case. Many fabricators have their own unique process for edging and tempering the glass. For best-in-class strength, durability, and low-distortion glass ask your fabricator about their tempering process, and if they have it, a quality handbook to see what specifications they adhere to.